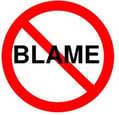
Where do we look? The Quality, Health, Safety and Environmental (QHSE) organizations can often be adjuncts to the “way an organization does its work.” Perhaps there are Quality or Safety moments, but they are not taken seriously, just a “check the box” activity. The most common finding is that QHSE is not integrated into every decision and work process throughout the organization.
In one of our engagements, a client had a major manufacturing accident in its European location. Accidents had happened before, but this one was different – it cost the company over $150 million. Therefore, the visibility was much greater than ever before. The Board was aware of such significant impact and wanted corrective action.
Step one was to challenge the status quo with a series of provoking questions:
1) How does your team’s QHSE behavior (or lack of) impact your ability to succeed in your role now? Why?
2) Do you have any roles and responsibilities or objectives regarding QHSE? If so, what are they?
3) To what extent does QHSE align with the Corporate direction (mission, vision, goals, objectives), and how?
4) Where is the Company today on a 1-5 scale in having a QHSE culture/behaviors? Where is your team? What would improve those scores?
5) Where do the Company and your team need to be on a 1-5 scale on having a QHSE culture? What are the key issues to improving the QHSE behaviors/culture? How do you measure it?
6) How frequently does your supervisor communicate about QHSE? How well do you understand your supervisor’s QHSE communications? What do you do differently as a result of those communications?
7) How many QHSE classes or seminars have you attended in the past year?
8) Where are the Company and your team today on a 1-5 scale on productivity? What would improve those scores? How do you measure it?
Warning Signs. In the aftermath of a major accident or in an organization feeling queasy about their QHSE culture, these questions will elicit some typical warning signs:
Overall Direction. QHSE is not part of the culture. It is not a focal point for the leadership team. QHSE efforts are not in alignment with strategy. Leaders are not aligned on communication, required communication, and action plans.
Operations. QHSE implementation varies by location. Inconsistencies exist between managers, supervisors, and employees. QHSE tools and procedures are used improperly or not at all. The daily focus on QHSE is insufficient.
Performance Management. People often know what to do but lack the motivation to do it. Effective incentives are not in place to promote the desired culture and behaviors. Supporting systems (compensation, job descriptions, performance agreements, etc.) are not in alignment with desired behaviors. Junior employees fail to grasp the risk, and supervisors fail to communicate either requirements or their justification
Where do you start?
- Implement a systemic approach that ensures the creation of an effective global QHSE culture
- Measure effectiveness of changes with metrics
- Focus on quick wins to promote the QHSE culture
The Roadmap:
- Treat the change as an organization transformation project.
- Establish a case for change that clearly defines the desired outcome, how it will be measured, and why it is nec
essary.
- Focus on process, behaviors, and a performance management system that rewards desired behavior and identifies non-conformance.
- Implement governance, accountability, milestones, and a process that deals with issues as they arise.
- Engage all levels of the organization through effective communications, training, and active solicitation of feedback.
- Measure outcomes and celebrate successes.
If you would like to discuss the various approaches and levels of support available, please use the contact form below.or contact me directly at gskarke@tbointl.com.